Muscle Shoals, Alabama, U.S.
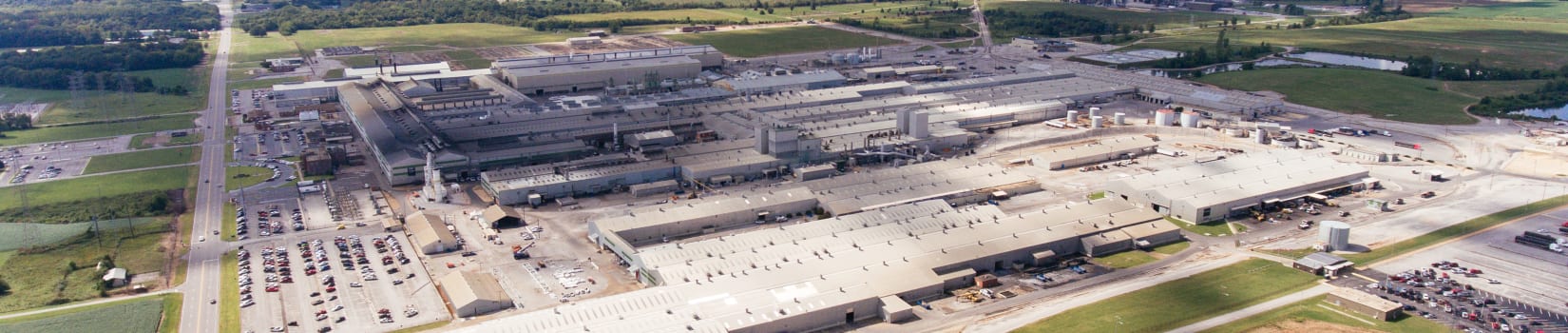
Constellium Muscle Shoals is a major aluminum sheet supplier for the packaging and automotive markets. The plant has ~1,250 employees and more than 100 acres under roof, including five casting units, hot and cold rolling mills, and a slitting and finishing center. Muscle Shoals produces aluminum sheet for use in all three components of beverage cans (body stock, coated end stock, tab stock) and has the capacity to produce over 1 billion pounds per year of finished aluminum coils. The plant also produces a to recycle 340,000 metric tons of aluminum, the equivalent of 25+ billion aluminum cans per year.
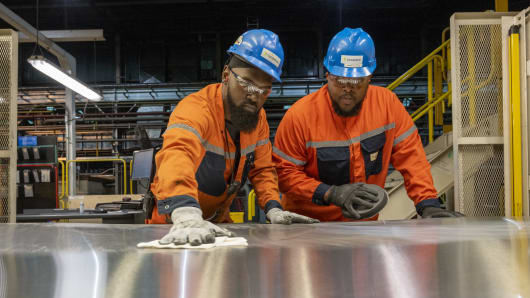
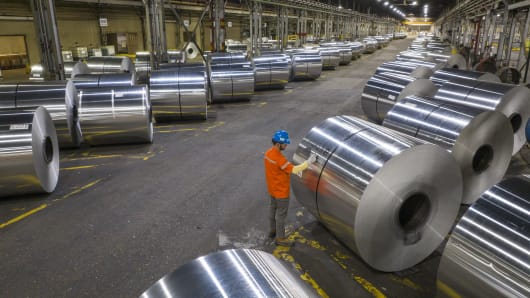
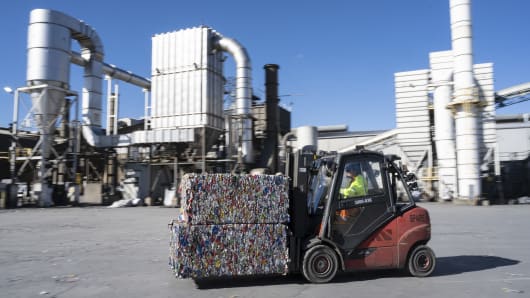
21
Job Openings
Talent across Constellium
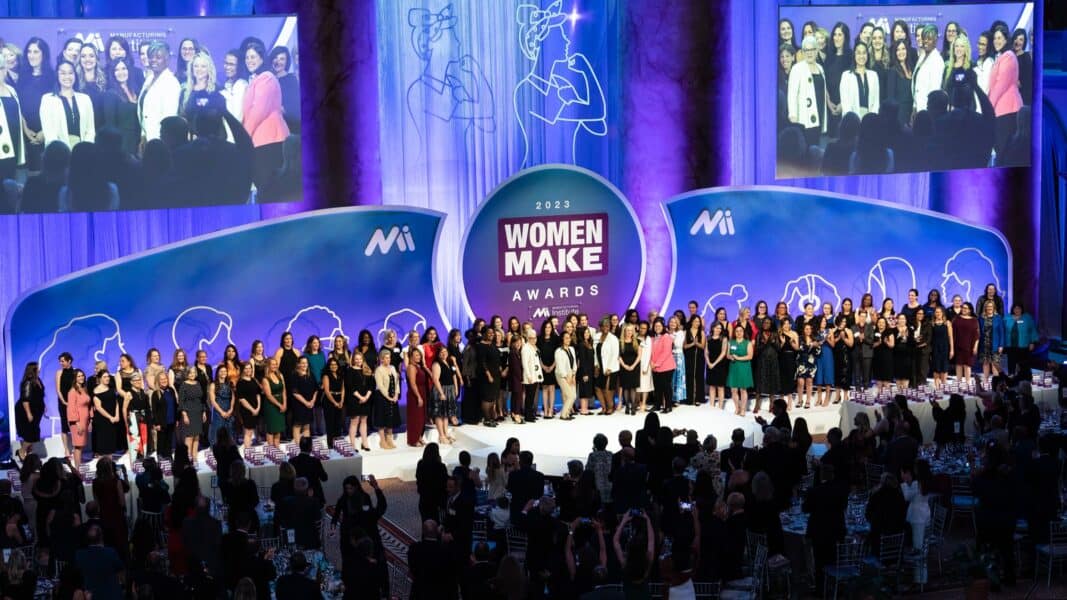
Constellium’s Anna Wilson Honored as an Emerging Leader at 2025 Women MAKE Awards
Constellium proudly celebrates Anna Wilson, Cost Analyst at our plant in Muscle Shoals, Alabama, who was honored as an Emerging Leader at the 2025 Women MAKE Awards Gala in Washington, D.C., on April 24.