Blog post
In 2009, the International Air Transport Association pledged to cut emissions from air travel in half by 2050, compared to 2005 levels.
Airplane makers are doing their part in the fight against climate change and addressing the concerns of environmentally conscious travelers. The aerospace industry is exploring a range of innovative technologies: new designs, alternative fuels, propulsion technologies, end-of-life recycling, and reducing emissions and waste generation during manufacturing.
It's a bird, it's a plane
Advances in materials technology and computing are opening the door to radical, futurist new designs for a more eco-efficient plane. These airplanes of tomorrow won’t be a common sight in the skies until at least 2030, but we can already take a glance at some of the concepts under consideration.
For example: morphing. This refers to aircraft geometry that actually changes while the plane is flying, controlled by receptors that can sense conditions such as temperature or airflow. The shape of the aircraft adjusts in nearly real time, making it more maneuverable, more fuel efficient—whatever the immediate objective requires.
Generative design is another new concept, using software to calculate extremely complex weight-to-strength ratios beyond the capacity of the human brain. It allows aviation engineers to take full advantage of 3D printing technologies and design bionic structures that are strong and light. Airbus has already used it to make a bionic partition in the cabin, and is expanding its applications to other parts of the plane.
And what if a plane didn’t have to look like a plane? Wings don’t have to be rigid. Planes don’t even need tails. As manufacturing methods such as 3D printing are making more complex shapes possible, nature—birds, butterflies, fish, stalks of grass—is providing designers with a wealth of inspiration, a concept known as biomimicry.
Airbus’ “Maveric” is a passenger plane resembling a stingray without a tail. Its disruptive design is known as a blended wing body configuration. Rather than use large wings to keep the fuselage aloft, the entire airframe provides lift. Unveiled in 2020, the Maveric is conceived as a reduced scale demonstrator for the blended wing body technology, aiming at a future full-scale airliner.
In 2019, Boeing unveiled its Transonic Truss-Braced Wing. It looks more like the type of plane we are used to seeing, though its lightweight wings are ultrathin and extremely aerodynamic, for greater fuel efficiency. A truss supports their wider span, and they fold almost in half to clear airport gates. Boeing says the new model will use up to 9% less fuel than traditional airplanes, and could be flying in about a decade.
Alternative energy sources
We don’t have to wait for tomorrow’s radical new airplane designs to see progress on sustainability today. Engineers are already working on alternative energies to decarbonize the industry.
One is electrification. To make an electric airplane viable, you need a small, relatively lightweight battery with a lot of power, ideally sustainably-sourced. We’re not quite there yet, though in the 1980s, the invention of lithium-ion batteries gave electrification an enormous boost. In 2015, they enabled the solar-powered Solar Impulse 2 aircraft to fly around the world in 16 months.
Most people can’t wait that long to reach their destination, and electric-powered jumbo aircraft that can cross the ocean are still years away. But lithium-ion batteries are well-suited to short distances, and it is likely that in the near future, electric planes will be common for commutes of up to 500 miles (800 km).
Numerous companies are developing electric propulsion for air taxis, commuter planes, and electric vertical takeoff and landing vehicles (eVTOLs), many of them autonomous. Electric motor manufacturer MagniX, for example, is working with battery storage provider H55 to transform the Vancouver-based seaplane operator Harbour Air’s aircraft into an all-electric fleet. And the Israeli company Eviation has developed Alice, the world’s first all-electric commuter aircraft, with battery technology like that of a cell phone and a range of about 440 nautical miles (or ~500 miles / ~800 km).
Hybrid power is another way to go. In 2020, the U.S. startup Ampaire’s hybrid-electric Eel performed a 341-mile test flight (~550 km) with an electric motor in the nose and a conventional combustion engine in the back.
And then there’s hydrogen, which has great potential as long as it can be produced from low-carbon sources rather than fossil fuels. Airbus is investing heavily in the technologies required to power aircraft with hydrogen generated from renewable energy, hoping one day to use it to power jumbo jets over long distances without CO2 emissions. Boeing is also testing its own hydrogen-powered aircraft.
Aluminium - Ideal for the air
The aluminium industry is working closely with the aviation industry to address climate change now and in the future. At Constellium, our engineers are collaborating with OEMs (Airbus, Boeing, Embraer, Lockheed Martin, etc.) to find ways to decarbonize flight in a cost-efficient way. Two important features of aluminium, lightweighting and recyclability, are essential to the greening of planes. The design flexibility enabled by aluminium-based aerostructures is a key benefit when adapting airframes to house alternative propulsion technologies. In addition, aluminium alloys are ideal for hydrogen storage, as witnessed by their use in the tanks of space vehicles.
High-performance aluminium alloys already play a major role in the skies, and we are constantly developing new ones. You can find advanced aluminium alloys on outer wings, the center wing box, the fuselage and nose fuselage, the engine (including gear boxes), and the landing gear. Our Airware® aluminium-lithium alloys—developed for the rigors of space travel—have exceptional promise for lightweighting and durability, providing up to 20% more lightweighting than conventional alloys, and being infinitely recyclable. Airware® alloys are perfectly adapted to complex new aircraft configurations, from fuselages to wings of the future.
Of course, one of aluminium’s major advantages is its excellent recyclability. It is infinitely recyclable without a loss in properties, and recycling aluminium uses only 5% of the energy needed to obtain primary metal. In the automotive industry, manufacturers are increasingly designing with selective dismantling and recycling in mind. This approach should be applicable to aircraft as well. The ultimate goal is to be able to dismantle end-of-life aircraft by material and alloy group, then recycle the scrap in separate routes to avoid cross-contamination—one more step on a path to zero-emission aviation.
So while we will have to wait a bit longer to fly on the futurist airplanes of tomorrow, we can still focus on materials and processes to decarbonize the planes of today. Fasten your seatbelts, the journey has just begun.
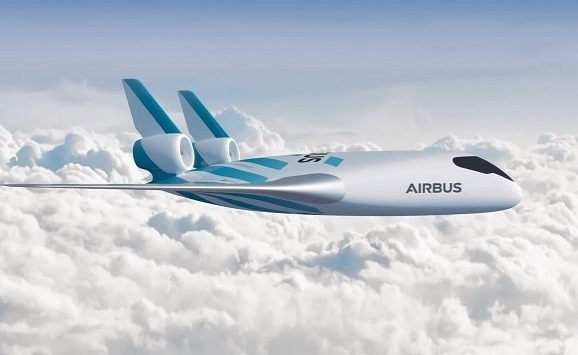
@Airbus
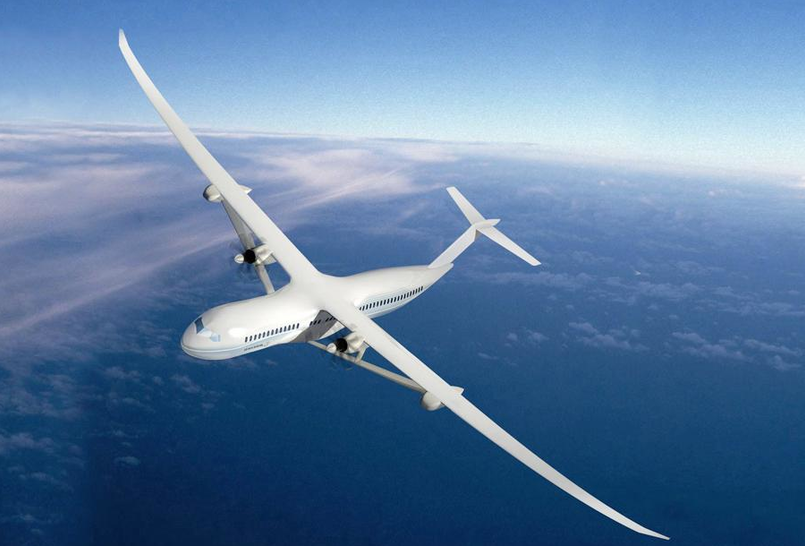
©Airbus
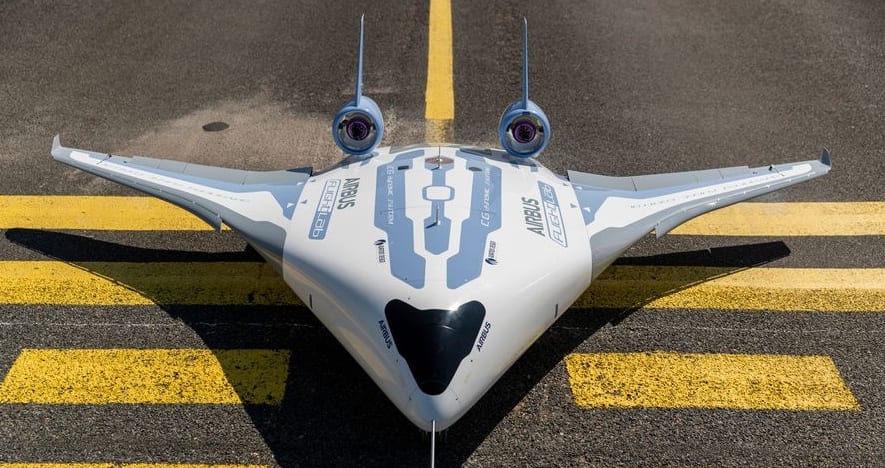
Boeing Sugar Truss-Braced Wing Aircraft Concept - ©Nhan Nguyen
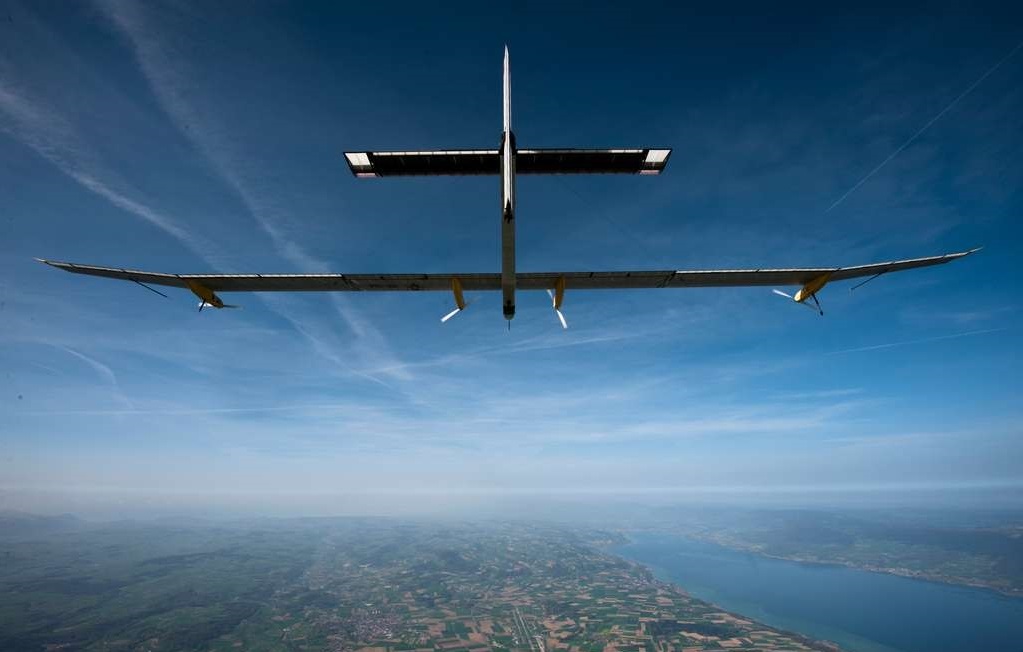
©Solar Impulse