Automotive Solutions
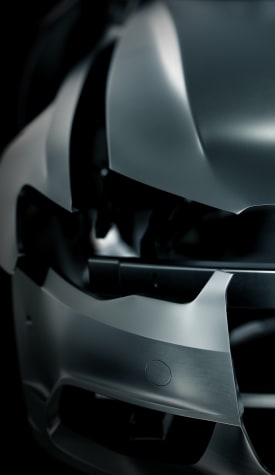
Driving Sustainable Mobility
Constellium stands out as a leading aluminum supplier with the unique ability to deliver both advanced rolled products and extrusion-based components for the automotive industry.
As a trusted partner and Automotive News Top Supplier, we help empower the world’s leading automakers with advanced aluminum solutions to shape the next generation of vehicles: lighter, cleaner, more sustainable, and built for performance.
From breakthrough materials to end-to-end support – including design, testing, and closed-loop recycling – we deliver the innovation and agility that drive sustainable mobility forward.
- of our 2024 revenue came from the automotive market
- 29%
- Crash Management Systems annual capacity
- 7+ million
- of Auto Body Sheet annual capacity
- 290k+ mt
Automotive Body Sheet
Constellium supplies a complete range of aluminum body sheet materials tailored for inner panels, outer skins, and structural parts. Our products are engineered to support the automotive industry’s shift toward lighter, more efficient vehicles – without compromising strength, safety, or visual quality. With advanced manufacturing capabilities and a strong track record of collaboration with automakers, we help customers meet their sustainability goals while delivering high-quality vehicles to the market.
Automotive Extrusion-Based Components
Constellium is a trusted supplier of advanced aluminum extrusion-based automotive components, engineered for superior safety and structural integrity. Our customized high-strength, and lightweight solutions are at the forefront of innovation, meeting the rigorous demands of automakers, while enhancing vehicle performance and sustainability. By partnering with our clients from the earliest stages of development, we deliver reliable and forward-thinking solutions that drive the mobility of tomorrow.
Automotive Specialties
Constellium brings deep expertise and a forward-thinking approach to specialty automotive applications. Whether enabling efficient thermal management with high-performance heat exchanger alloys or elevating vehicle interiors and exteriors through precision-finished decorative surfaces, our solutions are built for excellence. We combine advanced materials science with production know-how to help automakers push the boundaries of design, performance, and sustainability.
Battery Solutions
Aluminum’s thermal conductivity is about five times that of steel, making it the superior choice for thermal applications. For battery enclosures, aluminum sheets and extrusions provide a strong, crash- and intrusion-resistant exterior to protect the batteries that power EVs. Our technical teams are working closely with automakers to design modular battery enclosures that can be easily configured to fit various shapes and sizes, optimizing both design flexibility and manufacturing costs.