Transportation
Lightweight aluminum solutions for more efficient transport.
Lightweight strength is one of aluminum’s great qualities; in the transportation industry, every kilo saved contributes to our customers’ payload and fuel savings.
We have built upon the intrinsic properties of aluminum alloys to develop a range of dedicated extrusions, sheets, plates, precision sand castings, and semi-finished components for equipment parts within the transportation industry, such as tanker trucks, trailers, pleasure boats, trains, and trams. We minimize customers’ manufacturing costs and production throughput time with ready-made components, solutions, and personalized services.
We are a leading supplier to tank and trailer dump bodies and pleasure boats, and the market leader in large extrusion products for railway rolling stock.

Commercial Trucks and Trailers
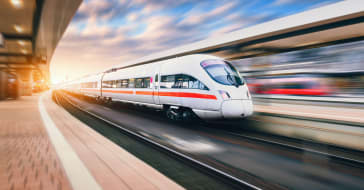
Rail
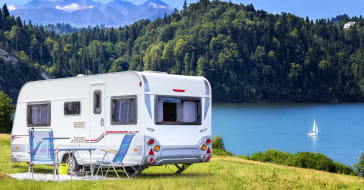
Leisure Vehicles
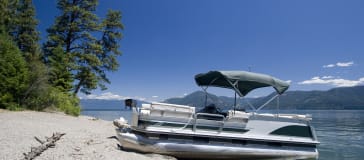
Pleasure Boats
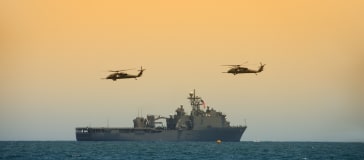
Marine
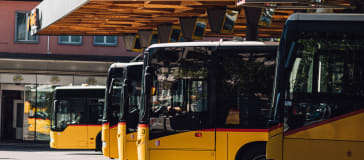