Blog post
Like the lead singer in a rock band, aluminium performs more brilliantly when it has backup support. In its pure state, the metal is too soft for most applications, but its intrinsic properties—low density, electrically conductive, corrosion resistant, formable, recyclable—make it a great base for developing high performance alloys.
Aluminium alloys refer to chemical compositions where up to 15% other elements (copper, silicon, magnesium, zinc, lithium…) are added to aluminium to enhance its properties, notably strength. Industrial applications often require a combination of several; these additions and the related heat treatments are what make each alloy unique.
Like following a recipe
One of the first major discoveries in aluminium alloys took place at the beginning of the 20th century, when the Prussian military was looking to make weaponry that was lightweight yet resilient. A German metallurgist, Alfred Wilm, discovered by chance that an aluminium alloy containing copper would harden if left at room temperature for several days.
Today, there are hundreds of different aluminium alloys, and an internationally recognized four-digit system for categorizing them according to their composition, from 1xxx through to 8xxx.
Making an alloy is not unlike baking a cake. Aluminium is melted in a large furnace, then other elements are added in precise quantities, where they dissolve like sugar in hot water. Once everything is mixed, it is poured into a mold, where it solidifies into ingots or billets (rectangular or circular sections of metal) weighing up to several tons.
These ingots and billets are either hot and cold rolled between two cylinders to form sheets, or else hot extruded (pushed through a die, like spaghetti) to form long parts in more or less complex sections. Finally, the alloy receives a thermo-mechanical treatment—it might be heated for a specific time and at a certain temperature to reach its desired properties, or else it is cold worked, for example by running it through a cold mill, which also makes it stronger. Some alloys use both processes.
Creating a new alloy
Applications for aluminium alloys range from rocket parts to sports cars, power lines, motorbike handlebars, cosmetic packaging, high-end smartphone cases, and more. Several items, even the simple beverage can, contain more than one alloy. Constellium offers a vast portfolio for all these different needs. When a customer asks for tweaks to existing alloys, the lab will test new additions or modify the treatment.
A bigger challenge arises when several parameters must be adjusted at once—alloying addition, processing temperatures and times—to meet multiple requirements, such as strength, corrosion resistance, and formability. Dr. Timothy Warner, Scientific Director at Constellium’s R&T center, says, “When a customer comes with a request we can’t directly meet, then the research community goes into action.”
Going to school
Universities are important actors in this research. Constellium frequently collaborates with the Materials Science departments at the University of Manchester and the Grenoble Institute of Technology, largely on pre-competitive work.
“Often with industrial processes, it’s difficult to interpret the physical metallurgy,” says Professor Philip Prangnell, from the University of Manchester. “It’s mostly incremental improvements through trial and error, which is slow and costly. But understanding the physics speeds up innovation and underpins process development across a whole chain of things: alloy composition, how it’s processed, and how that affects performance in the final product.”
Universities have the resources to look at a detailed problem over a long period of time. And while they don’t usually own industrial-scale rolling or casting equipment, they do have other very specialized (and very expensive) tools, as well as experts who know how to use them.
Looking inside in real time
Dr. Alexis Deschamps, from the Grenoble Institute of Technology, says that in recent years there have been two major changes in the field of material science. “First, the capability of seeing inside a material at a resolution that was not possible before—understanding how the atoms are organized. And second, thanks to computing possibilities, we can actually measure what goes on in real time, and watch it as it happens.”
For example, modern atom probes make it possible to peer inside aluminium and see how elements are distributed within an alloy at an atomic scale and in 3D.
Computer modeling has improved massively, so that now researchers can collect enormous amounts of data in situ. At the same time, there has been an explosion in the number of routes they can take to process the same materials and obtain different properties, shapes, and structures, for use in a variety of fields.
From research to applications
By understanding alloys on a nanometer scale, Warner says that Constellium has been able to modify the way they harden, with interesting results: “As a result of the understanding developed during work with Alexis’ team, we have developed a very high-strength aluminium lithium alloy (part of our Airware® family) which we’re currently proposing on the space market.”
Deschamps’ laboratory is also making use of their access to the Grenoble Synchrotron radiation facility to perform high resolution tomography, imaging alloys in 3D during simulated rolling, to see how quickly detrimental holes close during processing. This work has helped Constellium to optimize a thick plate alloy used in airplane ribs, the parts inside the wings that separate the panels.
Tomography can be equally useful in finding better ways to recycle aluminium—the most important way the industry can help reduce carbon emissions. The huge diversity of existing alloys complicates recycling efforts, since mixing different ones together can affect their properties. Prangnell says that tomography helps show the cavities when metals fail and tear apart. “You can understand how they nucleate. That teaches us how to optimize the material, to increase its toughness, so that recycled metals can tolerate more impurities and inclusions.”
Crafting the future
What advances can we expect for the aluminium alloys of tomorrow? Today’s scientists are looking for ways to reduce waste using new processing and manufacturing technologies, and considering how to reuse materials more often. Prangnell notes, “I can imagine cases where you use ‘dirty’ aluminum in the middle of a product, and ‘nice’ aluminium on the outside.”
Deschamps says he expects the field to separate into two major categories over the next 50 years. One would be efficient mass production for big industrial transitions, such as solar panel supports or electric car panels. The other would be tailored for unique, high-end finished products, “where you have one specific alloy for a specific application, with a specific additive manufacturing process, maybe one piece for one person, adapted for a watch, an iPhone, an F1 sports car.”
Warner dreams of finding aluminium-based solutions that are as sustainable and near carbon-neutral as possible. “Once you start asking yourself this question, you can see all kinds of opportunities,” he says. Other than that, he is happy to keep developing alloys for cars, planes, trains, and other objects around us: “It’s exciting seeing products you’ve worked on being used in the real world.”
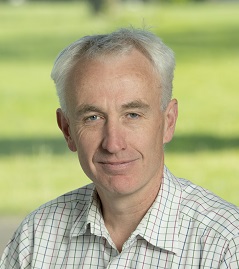
Timothy Warner is Science Director and Global Expert (metallurgy) at Constellium’s R&T center. He has been working for 30 years in the aluminium industry, in all stages of research and development, and is an inventor of more than 30 patents. In 2016, he received a medal from the French Academy of Air and Space for his contribution to industrializing Constellium’s Airware® technology (Al-Cu-Li alloys).
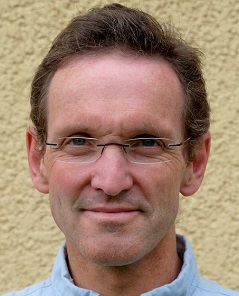
Alexis Deschamps received his PhD at the Grenoble Institute of Technology and has been a professor there since 1998. Prior to that, he studied Engineering at the Ecole Centrale de Paris and at McMaster University in Canada, and did a postdoc at the University of British Columbia. Deschamps has published close to 150 journal papers.
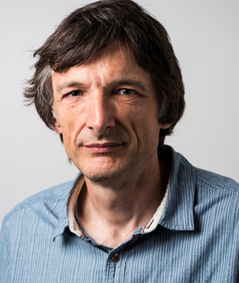
Philip Prangnell joined the Manchester Materials Science Centre after completing his PhD in Metal Matrix Composites at Cambridge University. His research activities are focused on studying advanced thermomechanical processing and joining techniques for light alloys (mainly aluminium and titanium). He has worked extensively with the aerospace industry on developing advanced manufacturing techniques for aerospace alloys.