Blog post
Humans build vehicles to withstand all sorts of challenging conditions: submarines that dive deep under the sea, race cars that drive full-speed for 24 hours, tanks that rumble through parched deserts. But it is hard to imagine an environment more brutal than outer space. Vehicles that travel into that region must resist extreme compression, severe turbulence, and unfathomable cold. They must be strong, lightweight, corrosion-resistant…and relatively affordable.
Our eyes on the Moon…and Mars
A decade after the Space Shuttle program ended, we are once again living through an exciting time for exploration of the heavens. NASA’s most important program of the moment is the Space Launch System (SLS), the most powerful rocket the agency has ever built. SLS will carry astronauts deep into the solar system, and is the only rocket capable of sending up to 130 tons of cargo and astronauts to the moon in one trip. NASA aims for a Moon landing by 2024, before setting its sights on Mars for 2030.
NASA has also been encouraging companies in the private sector to develop launch systems. As a result, over the past 15 years we have seen unprecedented interest in space exploration by non-governmental entities such as Elon Musk’s SpaceX and Jeff Bezos’s Blue Origin.
Outside the U.S., the European Space Agency is overseeing the development of Ariane 6, which will replace the trusty workhorse launcher Ariane 5. South Korea, India, and Japan, as well as Russia and China, are testing new launchers and vehicles, too.
Bank of America forecast would see the industry’s revenue grow 230% – from about $424 billion in 2019 to about $1.4 trillion in 2030.
Materials to take on the final frontier
A space launcher is a complex machine, to say the least. In a nutshell, it consists of cryogenic fuel/oxidizer tanks, pumps and fuel delivery systems, guidance and control systems, a rocket engine, and a payload module. Some launchers have solid fuel rocket boosters for an extra boost during the early stages of liftoff. Two-stage rockets use liquid oxygen or hydrogen for propulsion.
The materials used to build these rockets have exacting specifications, to withstand extreme environmental and operational stresses. For example, the propellant and oxidizer tanks of a liquid-fueled rocket are pressurized—and hold about two million liters of liquid hydrogen—so they require very high tensile strength (the maximum load that a material can support without breaking). Individual stages of space launchers are stacked on top of one another, and must resist compressive loading. There is enormous turbulence in the first stages of a launch, so launchers need a high tensile and compressive modulus to minimize flexing and bending.
Launch vehicles must not fracture when subject to extraordinarily low temperatures. Cryogenic oxygen, used in the current generation of rockets, is maintained at around -200°C, while cryogenic hydrogen, a propellant, drops down to -250°C. Moreover, launchers experience huge variations in temperature, with cryogenic liquid on the inside and ambient air on the outside. The current trend to design launchers with reusable components means that their tensile, fracture, and corrosion characteristics must not budge during reentry, when temperatures are exceedingly high.
Fuel tanks must be able to resist stress corrosion and cracking. When not flying around, these are stored for long periods in a tensile stress-inducing horizontal position, and often in coastal locations (such as Cape Canaveral) where the sea air is corrosive. And that’s not all: for ease of manufacture, metals used for space vehicles must feature good formability, machinability in T3X temper, and weldability.
At the same time, to achieve maximum payload and orbit options, a launcher must combine all this strength with very low density. The wall of a cylindrical fuel tank is only around 3-4 mm thick. “Visualize a giant Coke can,” says Michael Niedzinski, Group Leader Space and Defense, Director of Standardization at Constellium. “The strength of the material is extremely important.” Since the cost of launching cargo into space is astronomical, up to $5,600 per kg, it is important that the metal be cost-efficient, too.
Airware® soars higher
Thanks to its light weight and low cost, aluminium has been a favorite material for building rockets since the beginning of mankind’s adventure in space. Practically every early design for cryogenic fuel tanks and space launcher components used aluminium alloys 2014, 2219, 7050, or 7075. Though still dependable, these alloys are now 40 to 70 years old. Newer aluminium-lithium alloys have since come along, offering heavier payloads and higher orbits.
Constellium has developed several of these ultra-high performance alloys, grouped together under the Airware® brand. Responding to multiple challenging space launch requirements, Airware® offers higher strength, enhanced damage tolerance, and corrosion resistance, as well as lower density. It allows for a dramatic increase in payload capacity and higher orbits.
In the 1990s, Constellium, then operating as Reynolds Metals, worked with Lockheed Martin and NASA to develop a high-strength 2195 alloy with what Niedzinski calls a “cocktail” of elements: aluminium, lithium, copper, magnesium, silver, and zirconium. Airware 2195 replaced the legacy 2219 aluminum-copper alloy resulting in more than 3000 kg in weight savings. This technology was critically needed for a new generation of space shuttle rockets that delivered components to the International Space Station.
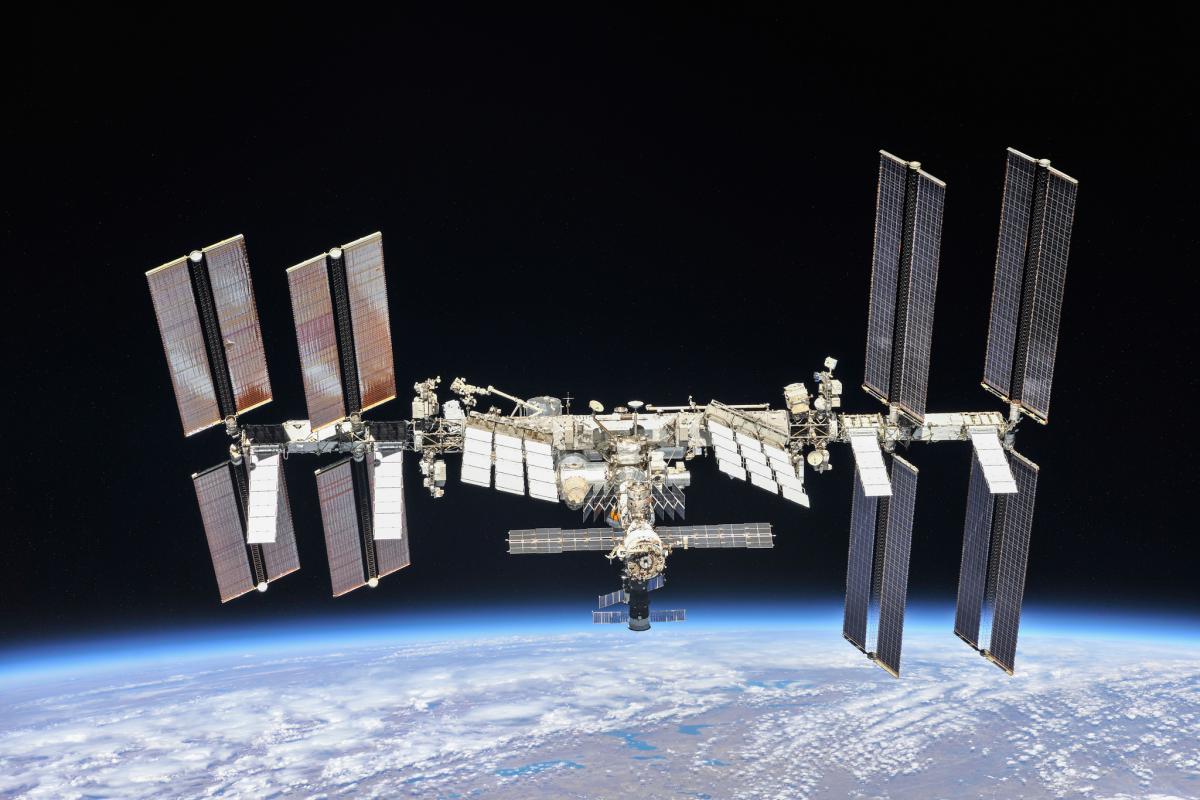
In this image from October 2018, the fully completed station continues its mission to conduct microgravity research and experiments — ranging from human physiology to astronomy aboard humanity's only orbital laboratory.
Image Credit: NASA
In 1994, the 2195 alloy was selected for the cryogenic sections of the Super Light Weight External Tank (SLWT), part of the early Space Shuttle launch systems. Over nearly two decades, 40 Space Shuttle missions used the SLWT to transfer large components to the International Space Station, something that would not have been possible without the re-engineered alloy.
Over the past 10 years, Airware® 2050 joined Airware® 2195 as a preferred plate material for pressurized and nonpressurized structural components of space launchers and crew modules. Both alloys were selected by major space programs – SpaceX’s Falcon Launchers, NASA Orion Crew Modules, and Boeing’s Space Launch System. Globally, several other space launch entities are performing studies and building prototype launchers using Airware® 2195 and 2050. Prototypes with complex shapes have been successfully tested for NASA’s Orion Crew Module, which will launch on the Space Launch System, taking humans farther than they have ever traveled before.
Once again, aluminium—the most abundant metal in the Earth’s crust—is helping us to blaze a path into the cosmos.