Our locations worldwide
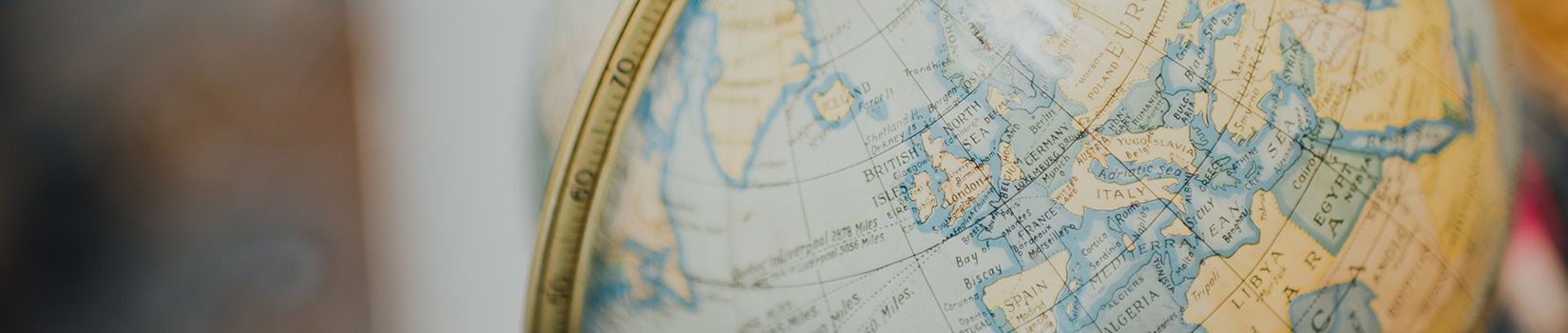
Baltimore, Maryland, U.S.
Corporate Office
Baltimore, MD 21202 - United States
Bowling Green, Kentucky, U.S.
Manufacturing Plant
Bowling Green, Kentucky 42101-8074 - United States
Brunel University, London, Uxbridge, United Kingdom - University Technology Center
R&D Center
Middlesex UB8 3PH - United-Kingdom
C-TEC, Voreppe, France - Aluminium Research and Development Center
R&D Center
38341 Voreppe Cedex - France
Changchun, China
Manufacturing Plant
Changchun 130103 - China
Dahenfeld, Neckarsulm, Germany
Manufacturing Plant
D-74172 Neckarsulm - Germany
Děčín, Czech Republic
Manufacturing Plant
Děčín 5, CZ-40502 - Czech Republic
Gottmadingen, Germany
Manufacturing Plant
78244 Gottmadingen - Germany
Issoire, France
Manufacturing Plant
63502 Issoire Cedex - France
Lakeshore, Ontario, Canada
Manufacturing Plant
Ontario N8N 2M1 - Canada
Levice, Slovakia
Manufacturing Plant
SK-934 01 Levice - Slovakia
Montreuil-Juigné, France
Manufacturing Plant
49460 Montreuil-Juigné - France
Muscle Shoals, Alabama, U.S.
Manufacturing Plant
AL 35661, Alabama - United States
Nanjing, China
Manufacturing Plant
Nanjing, 210038 - China
Neuf-Brisach, France
Manufacturing Plant
R.D. 52, 68600 Biesheim - France
Nuits-Saint-Georges, France
Manufacturing Plant
21702 Nuits-Saint-Georges - France
Paris, France - Headquarters
Corporate Office
75008 Paris - France
Plymouth, Michigan, U.S. - Aluminium Research and Development Center
R&D Center
Plymouth, MI 48170 - United States
Ravenswood, West Virginia, U.S.
Manufacturing Plant
West Virginia - United States
San Luis Potosí, Mexico
Manufacturing Plant
San Luis Potosí, SLP 78423 - Mexico
Singen, Germany
Manufacturing Plant
D-78224 Singen - Germany
Valais, Switzerland
Manufacturing Plant
3960 – Sierre - Switzerland
Van Buren, Michigan, U.S.
Manufacturing Plant
Van Buren Township, MI 48111 - United States
Vigo, Spain
Manufacturing Plant
36400 O Porriño-Pontevedra - Spain
White, Georgia, U.S.
Manufacturing Plant
Georgia 30184 - United States
Zilina, Slovakia
Manufacturing Plant
Gbeľany 013 02 - Slovakia
Zurich, Switzerland
Corporate Office
Zurich CH-8048 - Switzerland